PP hollow sheet extrusion production line
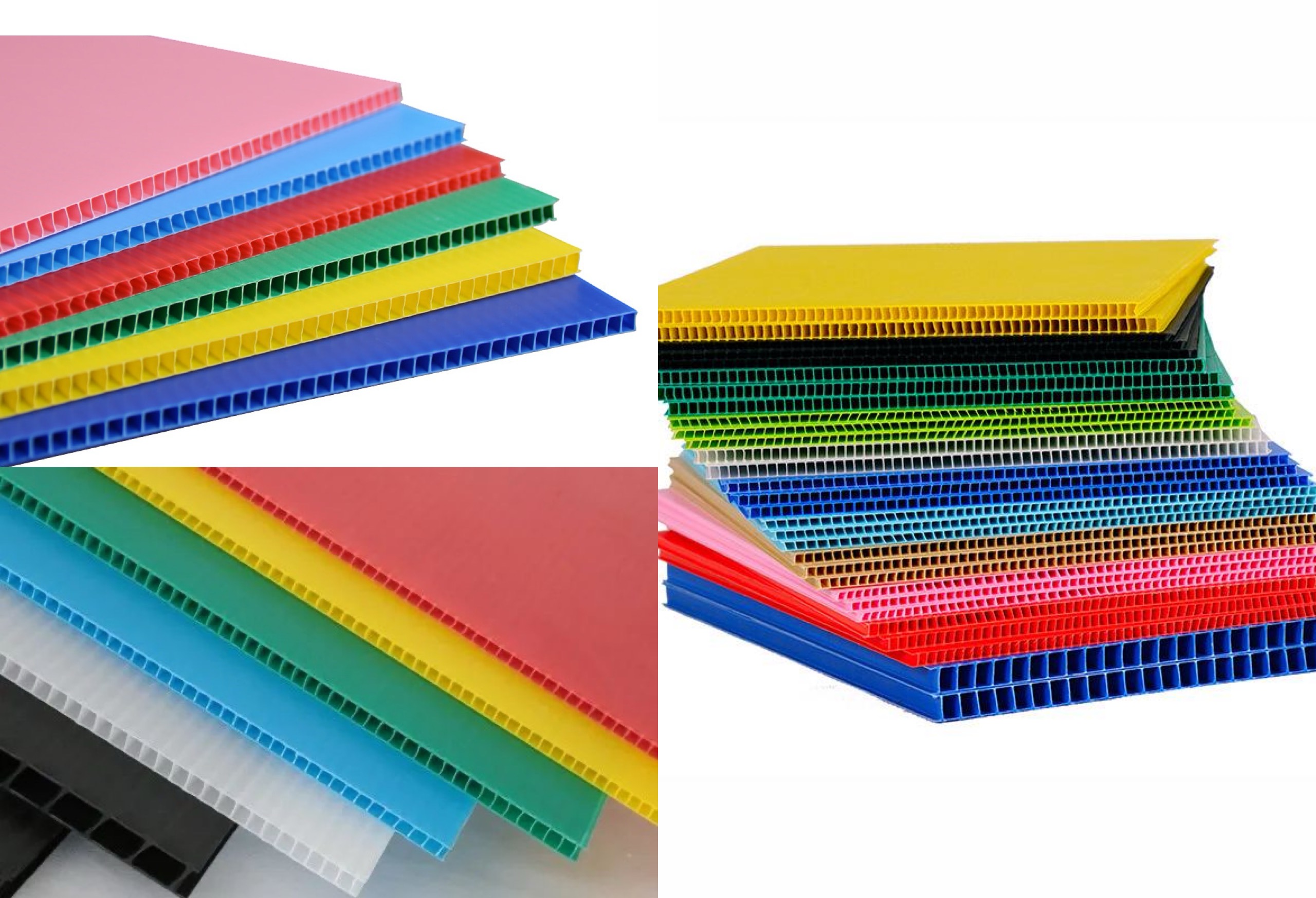
PP hollow sheet is a lightweight hollow structural board made of Polypropylene as the main raw material through the extrusion molding process. Its cross-section is lattice-shaped, with both high strength and lightweight characteristics, and is a new type of environmentally friendly material.
With the increasingly obvious trend of PP hollow sheet replacing corrugated cardboard in the packaging field, the market demand for PP hollow sheet has shown explosive growth. Traditional 1220mm, 2100mm and other sized PP hollow sheet production lines are increasingly difficult to meet the market and customer requirements for products. Problems such as small width and low output not only occupy the production cost of the enterprise, but also limit the business expansion of the enterprise. JWELL Machinery took the lead in launching a 3500mmultra-wide Pp hollow sheet production line to greatly increase the product width, fill the market gap, and help the development of the industry.
Advantages of Jwell Ultra-wide PP hollow sheet extrusion production line
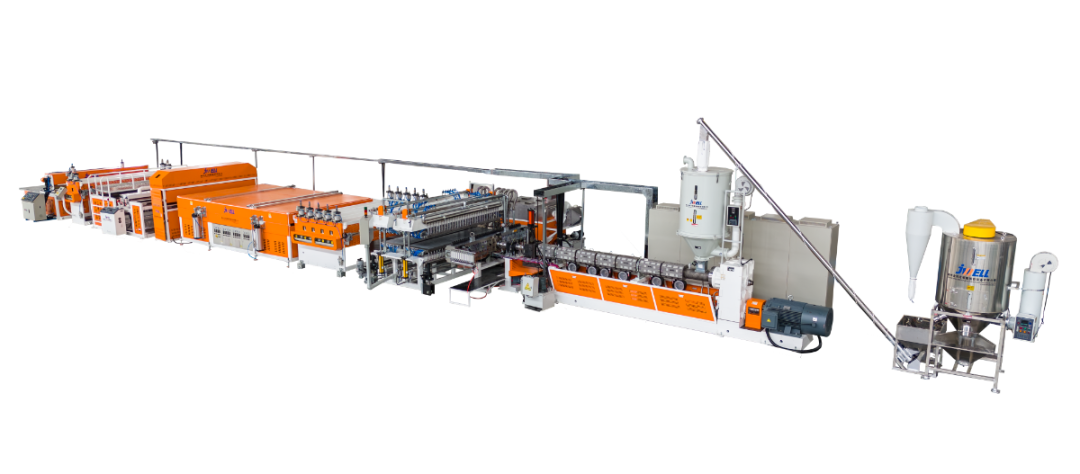
Advanced extrusion system
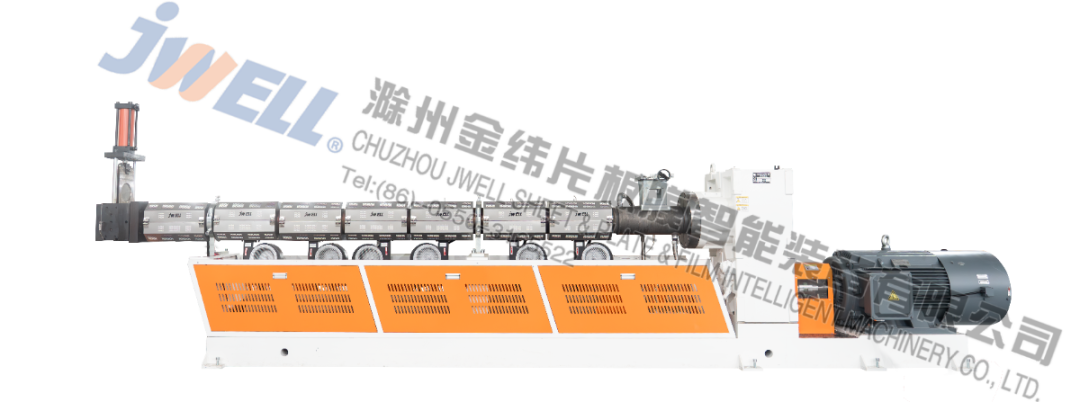
The newly designed screw structure ensures the plasticizing efficiency of the material and the stability ofthe output. Precise siemens control system, screw speed can be automatically closedloop control, to ensuregood plasticization of raw materials and high output and stable extrusion.
Unique molding and cooling system
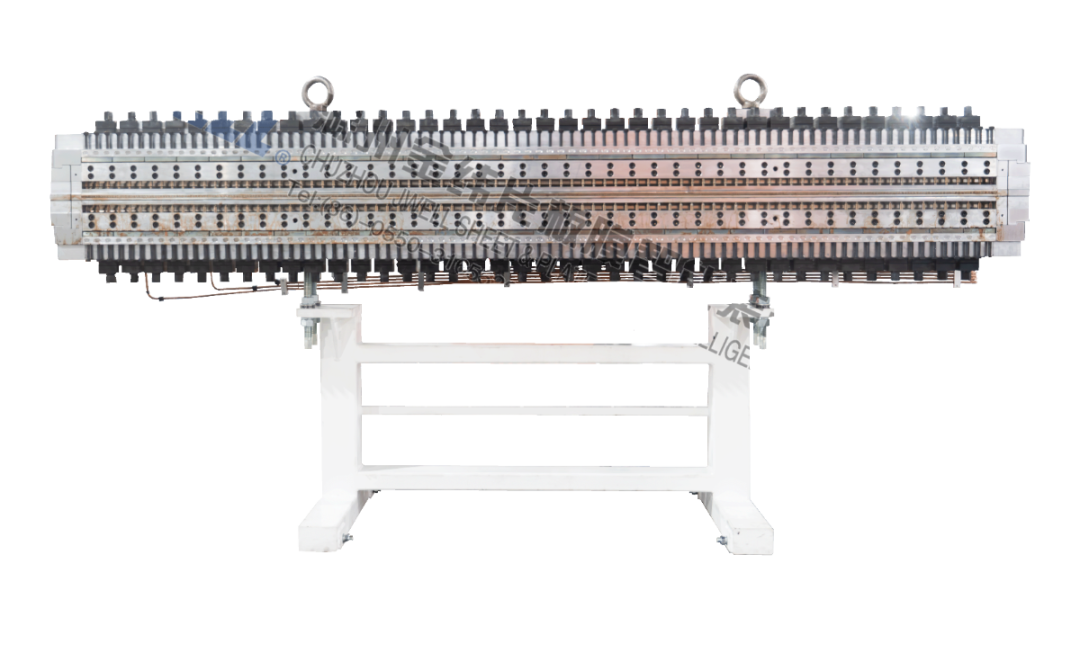
In the production of ultra-wide hollow sheets, extrusion molding and cooling shaping are the key to whether the products are perfect. How to solve the problems of bending, deformation, arching, wave, and vertical rib bending in ultra-wide production? Jwell Machinery adopts extrusion molding and vacuum cooling shaping systems with proprietary technology.
Mold steel imported from Germany, Jwell Machinery's unique flow channel desien.The mold
with a highly active throttling device to make the material flow pressure uniform in the die; the upper anelower dies are flexible to adiust, ensuring the uniformity ofthe upper and lower wall thickness.
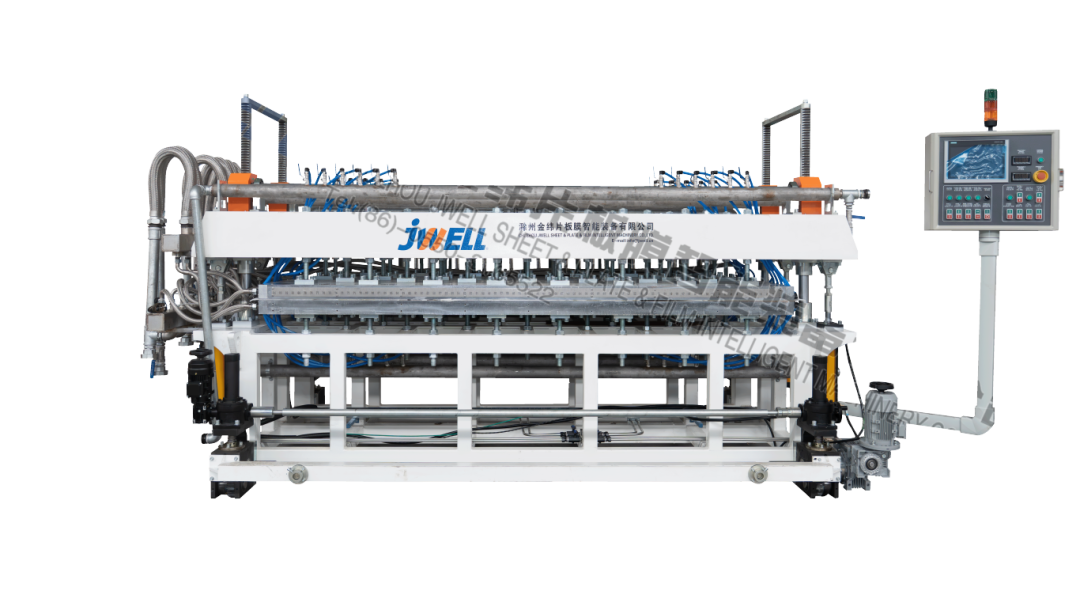
The aluminum vacuum setting plate and the surface are specially
light in weight and high in heat exchange efficiency. The vacuum system consists of two independent subsystems, each of which is equipped with an independent cooling water and a variable frequency vacuum adjustment system, so that the vacuum cooling can be flexibly adjusted according to the customer's productionsite.
Intelligent control system
l he production line is controlled by Germany Siemens PLC and is equipped with a rich human-machine interface. All process parameters can be easily set and displayed through the touch screen, and the operation is simple and intuitive. The production line has intelligent closed-loop control, which automatically adjusts the extruder pressure and production line speed. In addition, the control system also has an automatic fault diagnosis function, which can promptly detect and solve problems that occur during the production process, greatly improving the stability and reliability of production, reducing manual intervention, and reducing production costs.
Characteristics and applications of PP hollow sheets
Protection and cushioning: pp hollow sheet has excellent mechanical properties, high compressive strengthgood toughness and impact resistance. Shockproof and impact-resistant, protecting products from damage during transportation.
Environmental adaptability: waterproof and moisture-proof, corrosion-resistant, anti-aging, suitable for humid or chemical environments. Acid and alkali resistant, insect-proof, fumigation-free, with a lifespan of 4-10times that of corrugated cardboard
expansion: anti-static, flame retardant and other properties can be achieved by adding functional masterbatch. Flexible processing, thickness and color can be adjusted according to customer needs, and the surface is easy to print and coat.
Environmental protection and carbon reduction: The material is 100% recyclable, in line with the national carbon peaking and carbon neutrality goals, and the trend of replacing corrugated cardboard and injection molding boxes is significant.
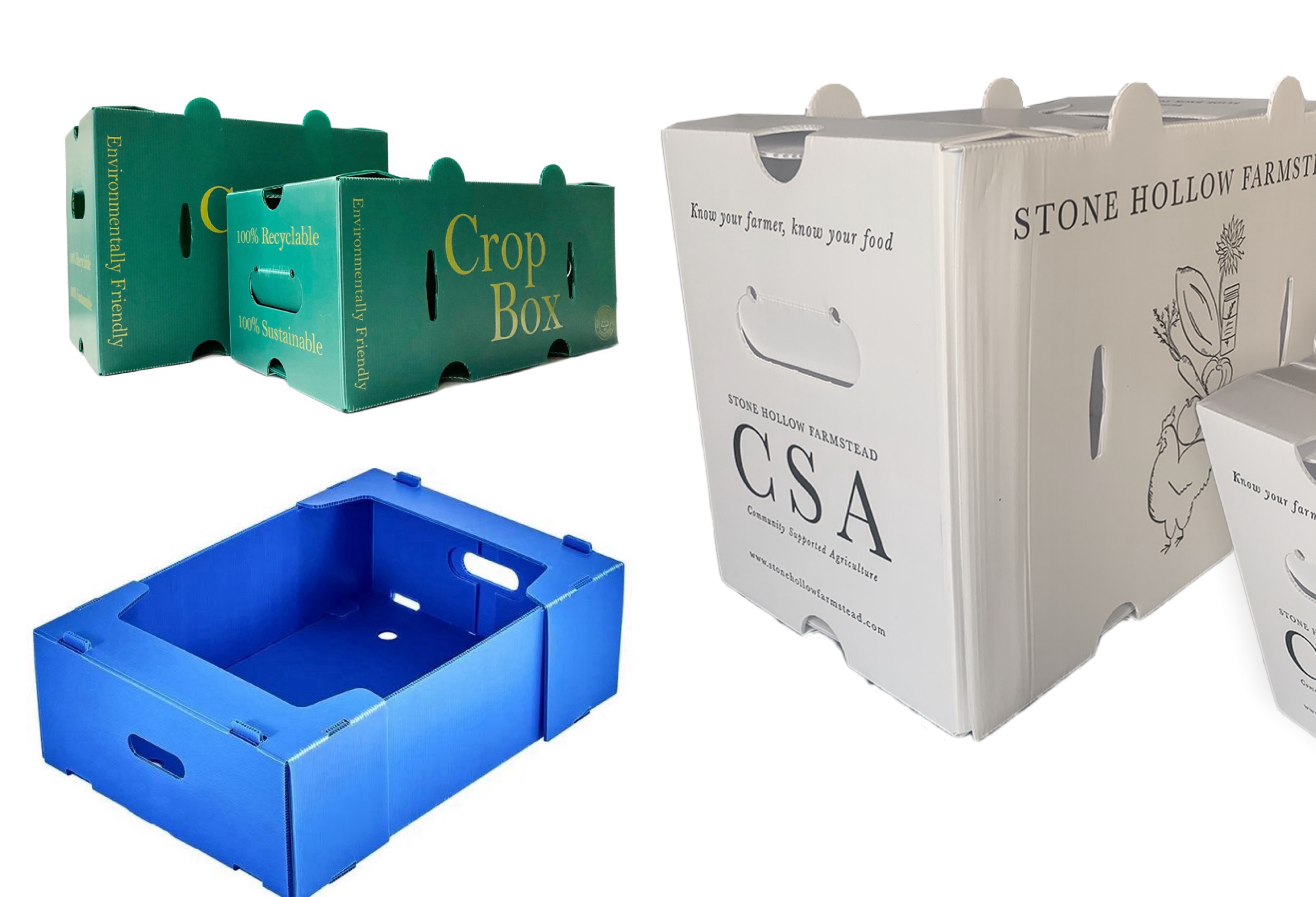
Application Areas:
Lightweight support: replace traditional boards (such as wood and metal plates) to reduce structural load.
Industrial packaging: electronic component turnover boxes, food/beverage boxes, anti-static knife cardsprecision instrument pads;
Advertising and display: display racks, light boxes, billboards (easy to print on the surface);
Transportation: automotive interior panels, logistics pallets;
Agriculture and home: fruit and vegetable packaging boxes, furniture linings, children's products.
Choose JWELL, Choose Excellence
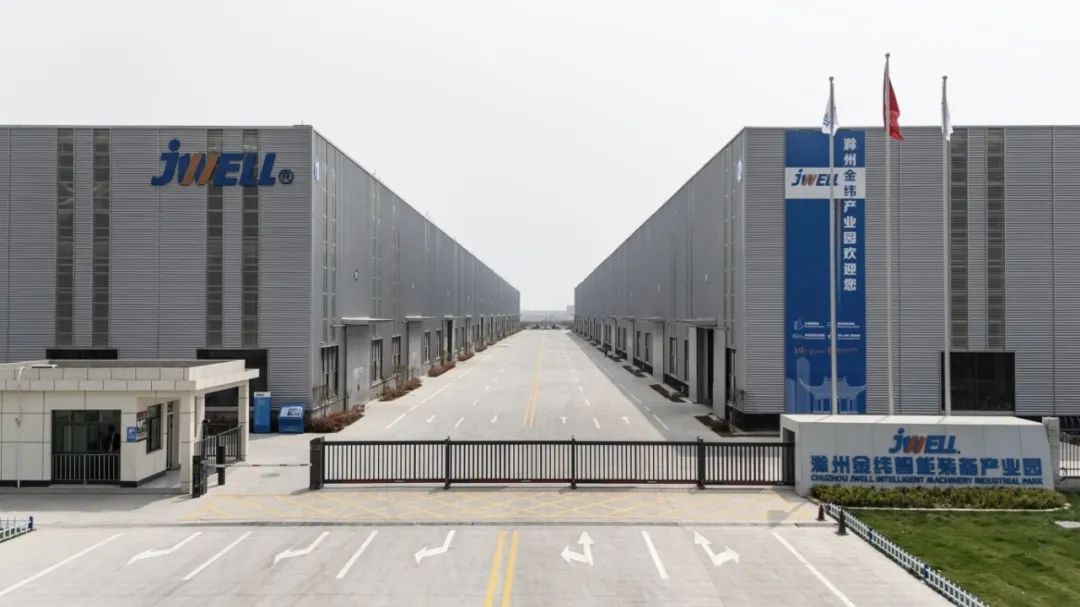
As a leading enterprise in China's plastic extrusion industry, JWELL Machinery drives industry development through global layout and technological innovation. At present, the company has built an industrial matrix of eight modern production bases and more than 30 professional companies, forming a full-chain system covering research and development, manufacturing, and services. With stable and reliable equipment performance, mature and superb process technology, and high-efficiency and low-consumption energy-saving advantages, our products are sold in more than 120countries and regions, making us a trusted plastic extrusion solution provider for global customers.
JWELL, Machinery always takes technological innovation as the engine and customer needs as the guide, deeply cultivating the plastic extrusion field. Whether in traditional plastic processing scenarios or emerging material application fields, we can provide you with adaptable intelligent and professional production lines.
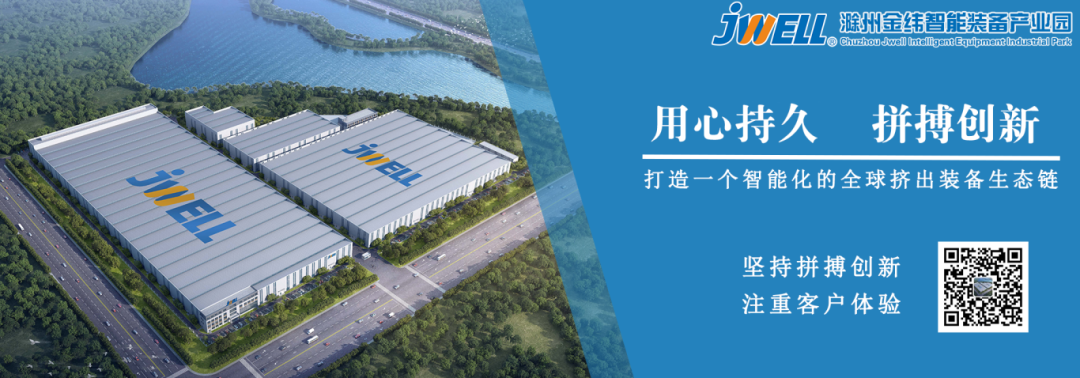
Chuzhou jWELL welcomes all new and regular customers to inquire . We will customizethe exclusive plastic extrusion scheme for you with professional team and high-qualityservice.
Post time: Jul-03-2025